MES(Manufacturing Execution System/製造実行システム)とは、製造現場レベルでの計画、指示、監視、データ管理を支援する情報管理システムです。下図における緑色のエリアを担います。生産管理システムなどの上位システムと製造設備との間に位置し、製造における情報管理の要(かなめ)になります。MESはMOM(Manufacturing Operations Management)と呼ばれることもあります。
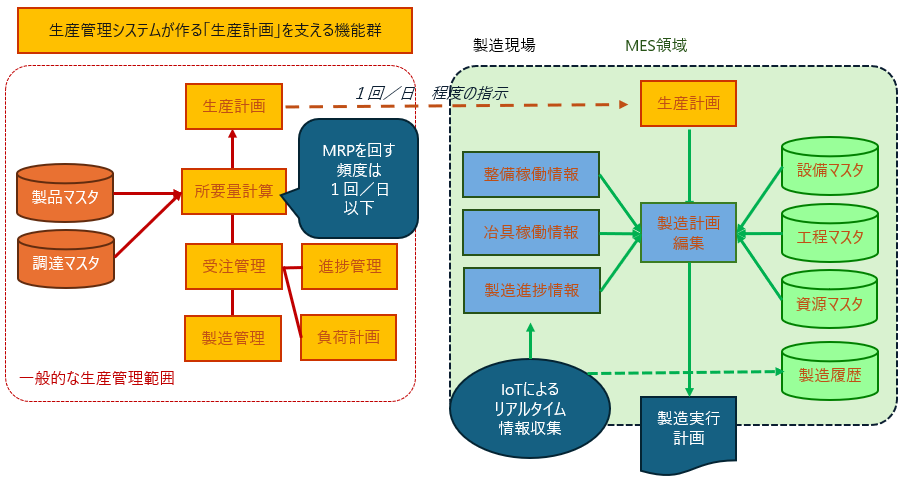
Techspireが考えるMES導入の第一歩
MESの導入で最も重要なことは、様々なMES機能の基となる情報の準備です。これはM-BOM(Manufacturing-Bill of Materials)と呼ばれるものであり、対象工場の設備能力、製品ごとの製造プロセス(BOPとも言われる)とその工程で使う工具・冶具・加工プログラム、検査・テスト情報、作業者段取り情報などの集合体です。もちろんこれらは、量産設計と試作で詰めた最終データであり、その工場に蓄積されたノウハウのデジタル情報です。工場(会社)ごとにそのノウハウは独自性があるでしょうから、それを体系管理するためのデータ構造もそれぞれに異なるでしょう。この情報群をデータベースに整理登録したものがM-BOMであり、MESが製造計画を策定する際に参照、段取りなどの作業指示書に反映させたりします。この情報の準備がMES導入に必須です。
生産管理システムとMESの管理粒度
上位のレイヤーに位置する生産管理システムが製造部門に出す指示は、ある程度の数量をまとめたロット指示が多くなります。この指示に基づき(ときにスケジューラを使い)製造指示を編成する時、パーツの供給・移送単位であったり、1回で可能な段取り数などの設備制約によって、管理する数量をロット指示の数量から変えたくなる(ロットの分割)と思います。この製造単位で作業指示書を出すということは、これが現場でのシステム管理粒度となります。指示に対して一対で把握するべき現場での工程(完了)実績の収集作業は、この管理粒度で実施することになります。理想の管理粒度は、1品1品なのですが、それは実績を報告する作業者の負荷を増やすだけでなく、情報システムへの負荷も増します。しかしIoTの活用による自動実績収集の実現や、それに対応できる情報システムが備われば、きめ細かな情報履歴を持って品質・生産性の向上などの効果を期待できます。このようにMESが管理粒度を分割したとしても、最終的には生産管理の管理粒度に合わせた実績に編成した報告を行うことになります。
製造履歴管理とトレーサビリティ
製品出荷後の障害原因の追跡には、製造情報の蓄積があれば効率的に行えます。製造プロセス(工程)とその実績収集に掛ける情報管理のためのコストを考慮すると、製造情報の管理(蓄積)粒度を闇雲に最小化することがベストだとは言えません。また、一品単位の管理がコスト的に許されても物理的に管理IDを付与できない場合はソフトトラッキングの手段を講じなければなりません。今以上に現場で流れる(動く)「モノ」と「情報」をズラさないで(できれば粒度を細かく)同期させて管理・蓄積することができれば、それが履歴管理の最適化でありトレーサビリティの実現となります。
暗黙知の形式知化は非常に難しい
戦後の団塊の世代が一斉に退職する時期が2007年から始まることを控えた2000年頃に、この「暗黙知の形式知化」がブームになりました。これに取り組まなければ、現場の熟練者の技が次世代に継承できない危機感をつのらせたためです。多くの研究機関や企業が、この問題に取り組みました。この時の成果は現在も企業内で活用されていると思います。ただし熟練者の頭の中にある感性や感覚をデジタル情報に置き換えて、非熟練者でも再利用できる形式知化することはまだ実現できていません。分析技術の向上で物理現象を分析して複雑なモデル式を定義できた分野は、システムに置き換えることができました。つまり、M-BOMに登録する情報は、隠し技のようなこの暗黙知と言うよりは、手間を掛けた日々の加工実績の記録そのものです。
設備への制御プログラムの同期送信
工場フロアに分散配置された設備・機械(例えばNC工作機械が配置された)を部品の工程ごとに渡り歩く場合、前工程から入った部品加工のNCプログラムの準備は、製造指図書に基づき、NCのメモリー内にある場合はその頭出し、なければ通信による取得を作業者が行うことになります。共通パレットを用いて搬送機構が機械間をつないだ(連続)FMSの場合、ロットの変わり目に同期してNC工作機械の運転モードを一時的に変えて加工プログラムを切り替える作業を行いたいと思います。この場合、FMSの運転を管理するのがPLCであっても専用コントローラであっても、FMS内のワークの移動をトラッキングして、そのワークに合致したNCプログラムを送り込む制御を行います。このように高度な自動段取替えと連続運転を実現するためには、冶具とワークと工具、それにNCプログラムを煮詰めた上で高精度な段取りを作業者が行うと共に、進捗管理と設備制御が必須です。
工場全体の設備俯瞰制御とAGVやAMR
もし工場フロアにAGVやAMRの導入を計画したい場合、その制御(設計)はどの視点で行えば良いのでしょうか。仮に固定軌道搬送となるAGVの導入の場合、ワークの受け渡しステーション、待機ステーション、充電ステーション、すれ違いエリアなどを決めることは難しくありません。また、AGVのPoint to Pointの移動もAGV自身に任せられます。ただ、そのCall信号を出すのは設備ごとに勝手に行えば良いのでしょうか。次の加工を始めたくて、部品を載せたAGVをCallしたのに、AGVの空がなくて長時間待たされる可能性はあります。機械群とAGV群の状態を俯瞰的に見ていれば、設備内の工程進捗に合わせたAGVの運用がイメージできます。AMRの場合、固定軌道が無くてルート自由度が増す分、設備との連携ポジション調整などは緻密さを要します。また、設備稼働率を向上させるAMRの運用に全体を俯瞰的に制御するシステムが必須であることに変わりありません。
工具管理とM-BOM
製造対象物や製造工程によって、また企業文化によって「工具」と呼ぶToolは多岐に及びます。このコラムでは、切粉を出す切削工具を対象にします。この切削加工は、ミクロ的に見れば工具の刃がワークに対して剪断破壊を連続して発生させているもので、工具自体が回転(例:フライス加工)するまたは直線的に動く(例:ブローチ加工)もの、あるいはワークが回転する(例:旋削)ものなど、この刃とワークの相対動作で行うものです。故に、刃先には相当な負荷が掛かるために摩耗します。この摩耗は、加工部位、対象素材、加工速度など、挙げればキリがないほどの多次元要素によって変動するので、画一的な条件を当てはめて管理することが非常に難しい現象です。刃先が摩耗した工具を使えば不良品を発生させるので、適切な工具交換を現場が行っています。この適切な工具交換は何を基準に判断すれば良いのでしょうか? 良くベテランのオペレータから聞くのは、「切削時の音」、「切削油の匂い」、などがありますが、誰もが身に着けているスキルとは言えません。やはり、製造指図書に記載する加工条件の中に、当該工具で加工できる最大個数や切削総合計時間などの記載を設けることが必要となります。この情報はM-BOMに登録する情報であり、多くの情報があればよりきめ細かな作業指示を作成できます。さて、加工品質の安定化を図る上で、現場での工具管理が非常に重要になります。前述のように摩耗した工具を交換するには、同一条件(径、突き出し長さ、その他)で揃えた工具が必要です。この工具の準備作業はどのような考え方で行えばよいのでしょうか。工場全体で共有する工具を専門部署が管理する体系。 部署(同じ系統の機械)で共有する工具を管理する体系。 機械単位または作業者単位で管理する体系など、管理の考え方は様々です。 工場全体の一括工具管理を始めたが、「IDを付けづらい」とか「工具の情報管理が追い付かない」などの悩ましい状況が続いた結果、システムを放棄して最後は作業者任せに帰結した話しを聞きます。工具は、ホルダ(機械との相性で決まる)とコレット、刃具(ビット)の3大要素の組合せを基とし、それに付属要素(アタッチメント)が加わることもあります。M-BOM(またはBOR:Bill Of Resource)はこれらの主要素を構造化ツリー形式で持ち、更に、クローン工具を準備する場合は管理小番を付します。これに装着できる機械種別(機械ID)や加工対象の製品や工程などをリンクします。さらにBOP(Bill Of Process)と共通で、加工プログラム、同時使用の冶具の情報や加工条件などもリンク(または保持)します。このようにM-BOMのなかで非常に重要な要素である工具情報を登録するには、現場での工具管理と運用(情報の更新手順など)方式が確立できていることが必須となります。
金型管理とM-BOM
高度経済成長期から1990年ころまで、日本は世界最大の金型生産量と技術を誇る位置に居ましたが、中国やアジア他国の技術の向上にともない徐々に生産量が減り、日本は超精密金型などの技術力を活かす方向にシフトしています。そのような技術を背景とし、日本は生産性向上での金型の活用巧者だと言えます。ご存知の通り、金型成形方式は同じ形状(部品)を大量に安く成形する方式に最も適しています。金型も工具の分類ですが、切削工具の種別以上に成形方式によって全く異なる構造になります。列記します。
- プレス金型
- 樹脂モールド金型
- ダイキャスト金型
- 鍛造金型
- 鋳造金型
- 順送金型
- 押し出し金型
金型も、そのタイプによって構成パーツがあり(鍛造型は例外)、切削工具のように使用時間が長くなれば摩耗するので、定期的なメンテナンスが必要になります。金型は小さな製品用でも非常に重量があり、保管場所から引き出して機械に設置する段取り替えも安全に留意した慎重な作業が必要になります。また、メンテナンス時には、金型を分解して個々の部品の補修(摩耗部への肉盛り、焼き入れ、磨きなど)を行い組み立て直します。金型を構成する部品の詳細な情報(部品番号、図面、CADデータ、製造者など)はE-BOMで管理することが多いと思います。よって、M-BOMは現場にある金型の情報をすべて(金型番号、保管場所、使用中、保管中、修理中などのステータス、使用時間、ショット累積数など)を管理します。